Riciclare le Bottiglie in PET per creare filamento per la stampa 3D
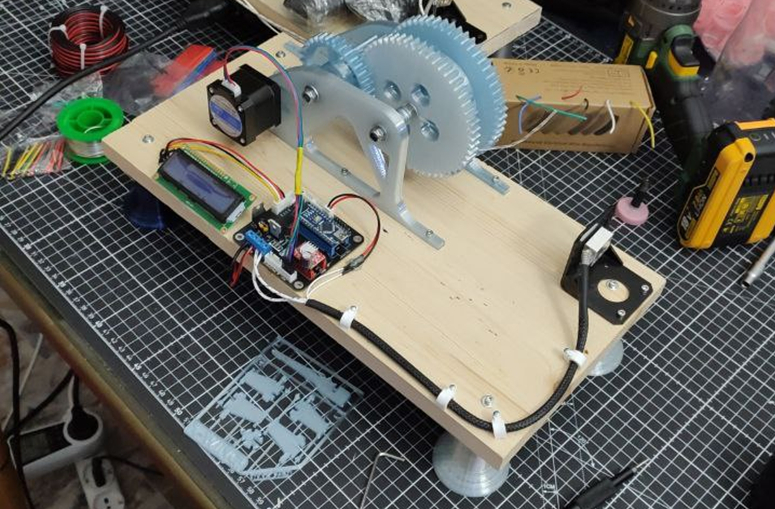
Negli ultimi anni, il mercato della stampa 3D è cresciuto in maniera esponenziale, aumentando anche la necessità di produrre filamenti adatti per dare forma alle infinite idee dei makers. La crescente consapevolezza ambientale ha posto il problema di ridurre l’impronta della produzione dei filamenti, magari riciclando gli scarti delle stampe per produrre nuovo materiale o trovare soluzioni alternative per produrlo in casa magari in maniera economica e soprattutto facile.
L’occhio quindi si è posato sulle bottiglie in PET, materiale economico che tutti abbiamo in casa (quanti di noi comprano bevande in bottiglie magari da più di un litro?), tant’è che negli ultimi mesi si è assistito a un vero e proprio boom di progetti inerenti a macchinari per trasformare questo oggetto d’uso comune in bellissima plastica da fondere e riutilizzare per stampare i nostri desideri. Fin qui parrebbe tutto facile, ma come mai non abbiamo ancora tutti questo macchinario per produrci in casa la plastica?
La risposta è presto detta, dei progetti opensource disponibili su internet, non ci sono macchinari “completi” al 100% che tengano conto di tutte le casistiche delle lavorazioni di polimeri, anzi, molto spesso questi progetti sono appena abbozzati. Come risultato si ottiene un materiale scadente, spesso quasi impossibile da stampare, fragilissimo, nonché in scarsa quantità rispetto le bottiglie utilizzate per prepararlo. Infine, questi progetti raggiungono dei costi talmente elevati da rendere praticamente senza senso la loro realizzazione.
Che Cos’è il PET?
Prima di iniziare a spiegarvi il riciclo del PET, è necessario spiegare di che materiale si tratta e di come viene utilizzato.
Il polietilene tereftalato, noto come PET, è una plastica comunemente utilizzata per produrre bottiglie e contenitori per alimenti. È apprezzato per le sue proprietà di leggerezza, resistenza meccanica e trasparenza. La sua diffusione massiccia ha fatto si che si creasse interesse sulla possibilità di riciclarlo industrialmente (insieme a polietilene e polipropilene, altri due materiali comuni nelle nostre case) ma ha anche generato un problema significativo di smaltimento dei rifiuti plastici, con conseguenze negative sull’ambiente. Sebbene in paesi sviluppati si riesca quindi a riciclare quella parte che non viene dispersa in ambiente, in molti altri paesi questo finisce integralmente in discarica o letteralmente buttato per strada. Il PET è chimicamente molto simile al PETG, una plastica molto in voga tra chi stampa in 3d per via delle sue caratteristiche di resistenza meccanica e termica superiori al PLA, ma che non necessita di una camera chiusa per essere stampato come l’ABS. Il PETG viene formulato appositamente per poter essere stampato ad una temperatura inferiore rispetto al PET, un requisito fondamentale fino a qualche anno fa in cui molte delle stampanti economiche e più diffuse non permettevano di superare i 250°C come temperatura di stampa. Oggi, invece, il mercato delle stampanti 3d si è evoluto e hotend (estrusori) con prestazioni superiori sono accessibili economicamente e compatibili anche con le stampanti più economiche. Il tempo è quindi maturo per permettere a tutti di poter stampare anche il PET!
Come viene riciclato il PET

Senza scendere troppo nel dettaglio del riciclo industriale, qualche precisazione va comunque fatta! Il riciclo industriale di questa plastica prevede diverse fasi, ognuna costosa in termini di risorse, macchinari e personale e può essere suddiviso nelle seguenti fasi:
- Raccolta del rifiuto nelle città; le bottiglie vengono buttate nel bidone della plastica insieme ad altri rifiuti di imballaggio (PE, PP, PS, PLA e tante altre ancora) e raccolte dai camion per poi essere portate ai centri di smistamento
- Separazione e pulizia; purtroppo, non si può riciclare tutta la plastica insieme (se non convertendola in energia nei temovalorizzatori) e quindi questa va prima separata per tipi di plastica (es. tutto il PET insieme, tutto il PE insieme e così via) e poi divisa ulteriormente per colore. Questa divisione è essenziale perché, se si mischiasse PET di bottiglie colorate, quello che otterreste è una plastica marroncina (come quando da piccoli mischiavate il pongo di vari colori) che certo nessuno utilizzerebbe per fare nuove bottiglie di plastica! (immaginate di comprare acqua in bottiglia marroncino). Infine, il PET così ottenuto viene sminuzzato per ottenere piccoli pezzetti facili da lavorare e viene lavato.
- Introduzione del riciclato nella produzione industriale; Le partite di PET adatto vengono poi portate negli impianti di produzione industriale e mischiate con della plastica vergine (e a volte altri additivi per migliorarne le performance) per produrre nuovi oggetti. Mischiare la plastica vergine con quella di riciclo è essenziale perché riciclandola, la plastica si indebolisce (subisce degli stress termici perché viene rifusa diverse volte e degli stress meccanici perché viene tagliuzzata e sminuzzata) e difficilmente può essere utilizzata tal quale per produrre un nuovo oggetto.
Leggendo questa lista è evidente che, perché abbia senso riciclare industrialmente, bisogna raccogliere grandi quantità di plastica, bisogna investire molto nelle infrastrutture, consumare molta energia per far funzionare tutte queste macchine e vi è un grande utilizzo di acqua! Senza contare quanta CO2 immettiamo per far girare i camion che, alla fine, riporteranno da noi quella stessa plastica che abbiamo buttato mesi fa! Un modo per ridurre quindi l’impatto ambientale del consumo di plastica (e del suo riciclo) passa quindi dalla riduzione del rifiuto stesso. Se la bottiglia viene riciclata in casa, questa non verrà trasportata in giro, non dovrà essere divisa, lavata e poi rifusa per produrre nuovi oggetti, diminuendo l’impatto di tutta la catena del riciclo.
Come riciclare le bottiglie – La PET Machine
Gianfranco, maker, studente di dottorato di ricerca in Materials Engineering and Industrial Biotechnology e tecnico presso il dipartimento DICAM dell’Università di Bologna, lavora da mesi nel combinare gli aspetti positivi dei vari prototipi proposti su internet, apportando spesso le sue personali modifiche, al fine di realizzare una macchina completa che sia economica da costruire, affidabile, facile da utilizzare e che realizzi un filamento il più perfetto e semplice da stampare possibile, affinando anche tutte le fasi di pre e post produzione, come la lavorazione della bottiglia prima del taglio tramite riformatura e l’essicazione del filamento per rimuovere l’umidità e rendere il filamento più resistente. La macchina è presentata in anteprima assoluta nella II Innovation Faire di Sovramonte, dove ha lavorato incessantemente per 3 giorni per produrre del filamento che, nel mentre, veniva stampato da una fantastica Prusa Mini (Grazie ancora Andrea di Prusa Research per averla prestata alla causa!)
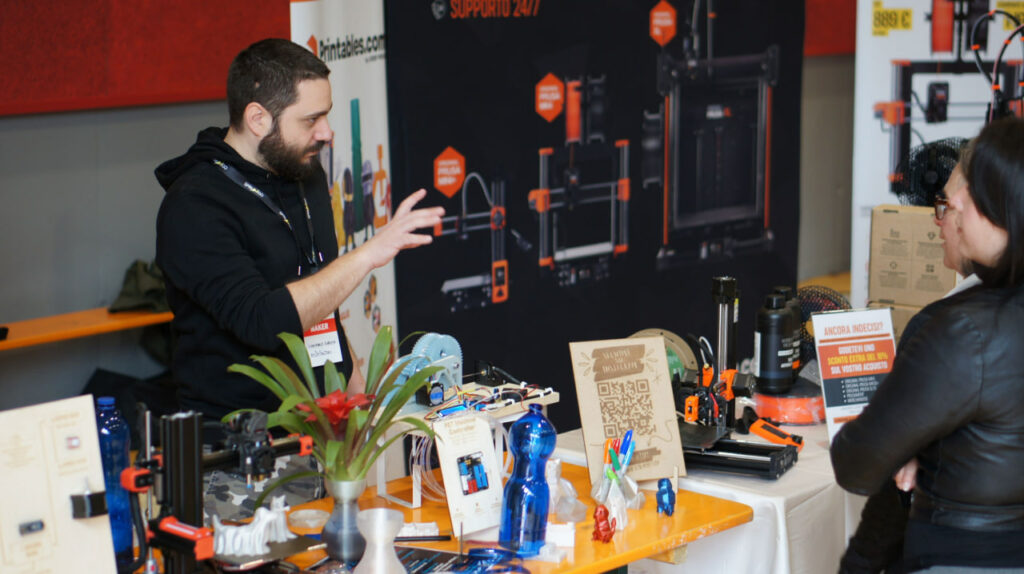
(con un banchetto pieno di cose stampate dalle bottiglie proprio in occasione della fiera!)
Le fasi del riciclo della plastica con la PET Machine
Il riciclo della bottiglia tramite la PET-Machine avviene in 5 fasi:
- Si raccolgono le bottiglie della stessa tipologia e si rimuove l’etichetta. Se necessario si rimuove il residuo di colla che era presente sotto l’etichetta (certe aziende ne mettono quasi nulla, altre invece hanno deciso che è meglio abbondare!)
- Si mette un poco di acqua dentro la bottiglia (bastano 1-2 dita) e si avvita sulla bottiglia un tappo in cui è stata messa una valvola (presa da una camera d’aria per biciclette) e si pompa dentro un po’ di aria
- Si scalda la bottiglia facendola ruotare per omogeneizzare le irregolarità delle bottiglie (punti strozzati dove la bottiglia è più sottile oppure punti in cui è corrugata); questo punto non è necessario per molte bottiglie che sono già cilindriche
- Attraverso un tagliabottiglia si prepara una striscia dallo spessore definito
- La striscia viene trasformata dalla macchina (attraverso il processo di pultrusione) che la porta a formare un cilindro (più o meno vuoto all’interno) che è già pronto per essere stampato in 3d.
Su internet sono presenti molti consigli e molte guide (scritte o in video) su come effettuare ognuna di queste fasi, con soluzioni artigianali discutibili che possono funzionare più o meno bene e che spesso introducono poi più problemi che altro. Fortunatamente, i mesi passati ad ottimizzare i vari passaggi hanno portato allo sviluppo di una procedura semplice che tiene conto anche di come poi verrà usato il filamento prodotto.
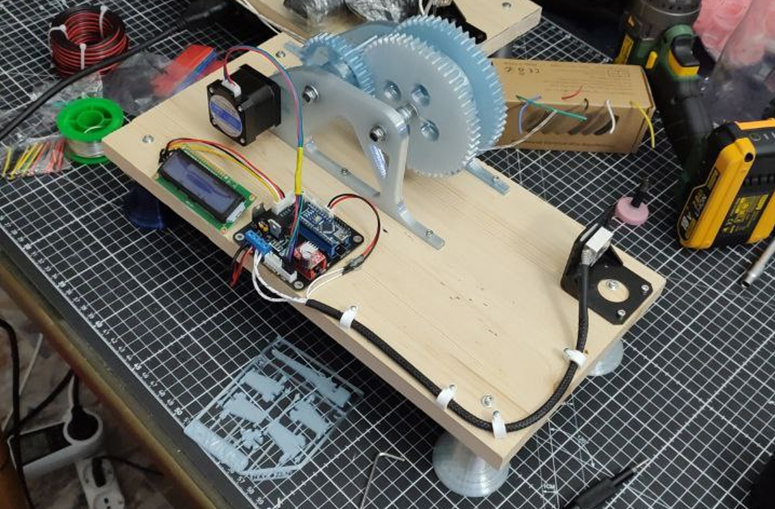
Il filamento prodotto può essere colorato (con uno o più colori) e per la sua produzione viene consumata una quantità minima di energia elettrica e acqua (la stessa acqua può essere travasata di bottiglia in bottiglia dopo che quest’ultima viene lisciata). Inoltre, si utilizza circa l’80-90% del peso della bottiglia (in quanto collo e fondo non possono essere trasformati in strisce) che viene poi stampata direttamente senza il bisogno di mischiarla con plastica vergine e riducendo drasticamente la quantità di plastica che viene buttata del bidone. Come ultimo valore aggiunto, gli scarti di stampa (stampe fallite, supporti, brim, ecc…) possono essere buttati nel bidone della plastica e verranno riciclati con il resto del PET raccolto in città! (cosa che non è possibile fare con ABS, ASA e altri tipi di filamento).
Il controller della PetMachine
Molti dei progetti presenti su internet, come dicevamo prima, sono costituiti da componenti costosi e da grandi quantità di pezzi in plastica (per fortuna almeno stampabili in 3d). Alcuni, per esempio, convertono stampanti 3d intere per sfruttarne l’elettronica (ma poi richiedono un complicato modo di controllare la macchina attraverso codici gcode appositamente elaborati) oppure scelgono l’uso di più microcontrollori per la gestione della temperatura e della movimentazione della macchina. Altri prevedono di stampare in 3d pezzi per pesi molto superiori al Kg, rendendo quasi impossibile recuperare il peso in plastica tramite le bottiglie se non nel giro di anni (una persona beve mediamente 1 bottiglia di acqua al giorno).
La PET-Machine è composta da pochi componenti scelti, quelli essenziali per il suo funzionamento ed il più economici possibile, uniti tra loro da una scheda plug&play costruita da noi sotto l’occhio attento di Gianfranco.
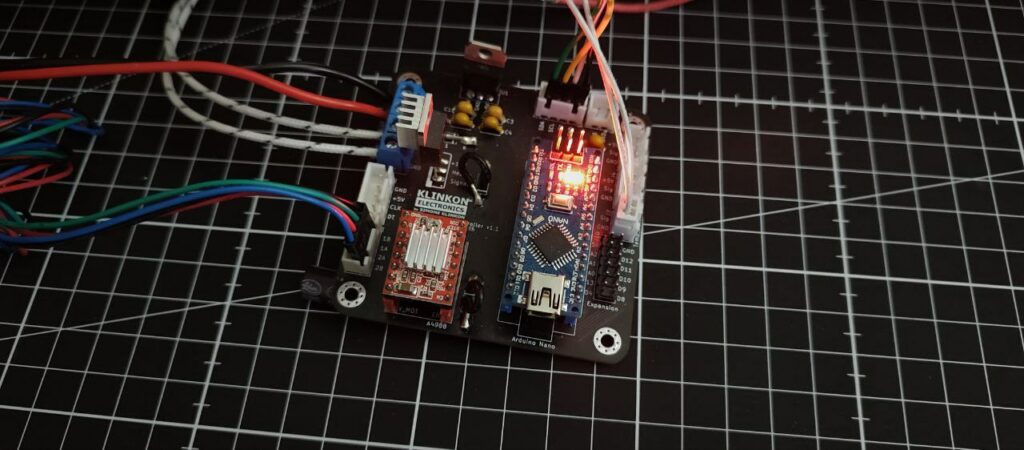
La scheda, basata su un Arduino Nano, gestisce la temperatura di un ugello modificato appositamente per piegare la striscia di plastica e darle una forma cilindrica del diametro per le stampanti più comuni (1,75mm), e gestisce la velocità del motore che avvolge il filamento così creatosi intorno la bobina.
Tramite un display LCD e due encoders è possibile regolare i parametri di temperatura desiderata e velocità, adattandole alle condizioni che potrebbero variare da bottiglia a bottiglia (ma tranquilli è meno complicato di quel che sembra! Tanta ricerca e ottimizzazione è stata già condotta da Gianfranco), oltre che avere un ampio range di personalizzazione grazie al connettore di espansione e possibilità di riprogrammarla a proprio piacimento.
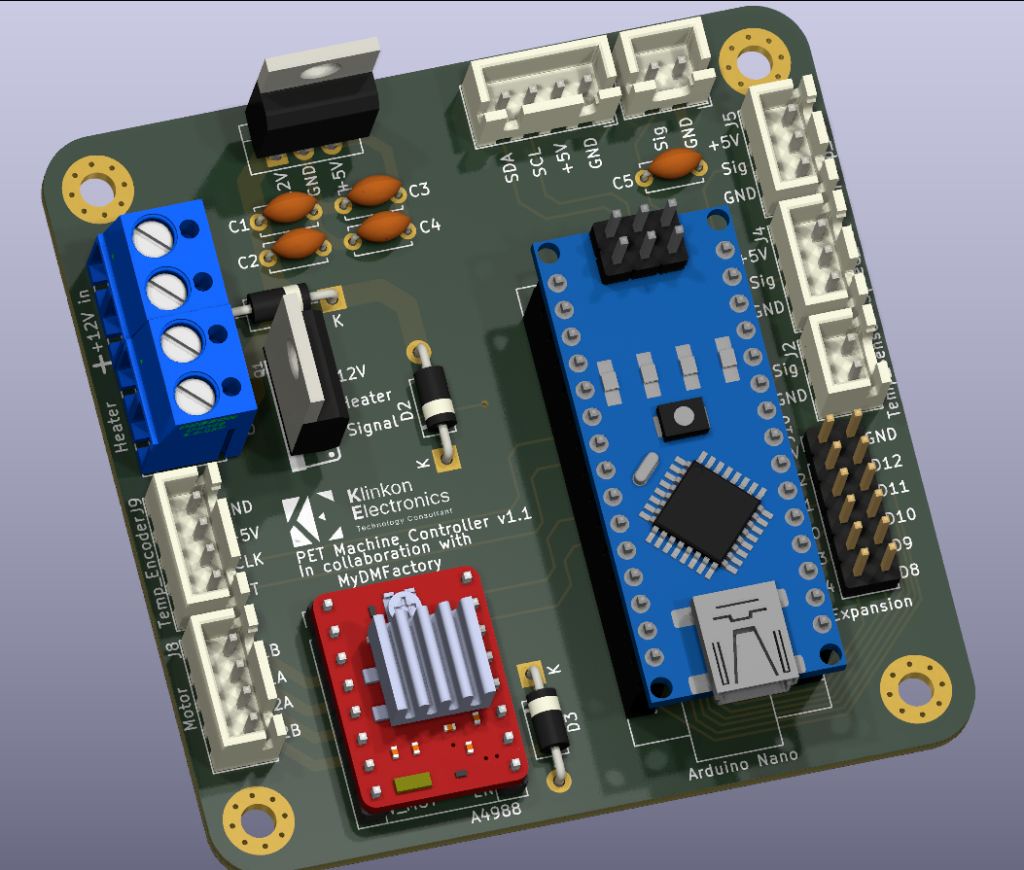
Il filamento così ottenuto va, ovviamente come ogni filamento per la stampa 3d, essiccato e calibrato (non dimenticate a testare il flusso di stampa, per fortuna una volta fatto il profilo, esso è valido per tutte le bottiglie dello stesso tipo). Le bottiglie sono state per mesi in contatto con l’acqua che contenevano ed essa, nel mentre, ha permeato la plastica. Per fortuna bastano poche ore (dalle 2 alle 4) a 50°C per essiccare il filamento e renderlo perfetto per essere stampato senza intoppi!
Sviluppi del progetto
Attualmente la macchina non è ancora stata rilasciata al pubblico, in quanto stiamo lavorando a diverse ottimizzazioni, a partire dalla scheda di controllo per arrivare al ciclo produttivo del filamento, che richiede ancora affinamenti.
2 risposte
Salve , il progetto rilasciato , sarà Open Source?
È ancora in fase di definizione il tutto, ma probabilmente si 🙂